Beer Grill AG
Thanks to customX, Beer Grill AG can accelerate the construction of display cases for the catering industry
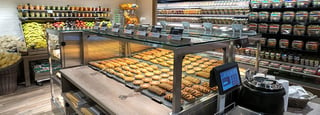
Caterers have to be flexible - also with regard to the presentation of food. Showcases support this flexibility. Beer Grill AG in Villmergen, Switzerland, wishes to meet the very specific requirements of its catering customers faster and more efficiently and has decided to use a configuration solution with customX. There was reason for optimism right from the introduction: an acceleration of the construction time by 30 to 40 percent seems realistic.
Targets
To design increasingly more complex products in an increasingly shorter time - Beer Grill was looking for a new configuration system that enables a high degree of automation and digitization, is directly linked to Autodesk Inventor and generates dimensional drawings and production documents.
Implementation
At the beginning, customX was used in parallel with a previously self-programmed system, but will completely replace the old system in the future. The entire product knowledge is stored in the system, so the sales department can create quotations directly on site. After a short training session, Beer Grill employees can maintain and expand the set of rules independently.
Conclusion
Beer Grill expects an acceleration of at least 30 to 40 percent. The employees' knowledge has been migrated into the system and is now permanently available to the entire company.
The Perfect Display
Whether canteen or restaurant, self-service or service - the food should be a feast for the eyes of the guests. A showcase must therefore present food in an appetizing way and maintain its quality: The soup should be hot, the salad fresh, the ice cream cold and the chips crisp. In addition, variance is required because guests may be offered a vegetable stir fry today, pizza tomorrow and barbecue the day after. Therefore, in addition to the technical and visual equipment, a wide range of accessories that can easily be exchanged is also important.
Innovative products for a demanding clientele
According to the motto "Keep room for tradition - make room for the future", Beer Grill AG in Villmergen, Switzerland, has technologically become the leading manufacturer of systems for the professional presentation and preparation of food. Beer Grill serves discerning customers throughout Europe and is constantly setting new quality standards in design, patented technology and functionality. Perfectly matched to the location, space and general conditions of the customers, the product range offers many possibilities. All the appliances are convincing due to their innovative technology and intelligent design and are able to ideally maintain the quality of the culinary offers.
A "classic" wins the race
Early on, the company had developed its own small modular design system and, a few years ago, also introduced Autodesk Vault for product data management. However, products are becoming increasingly more complex and have to be delivered in an increasingly shorter time. The company's own solution did not offer enough automation for these growing requirements; a new level of digitization was needed. The company was looking for new configuration software that would be directly linked to the CAD system in use, Autodesk Inventor, so that new dimensional drawings and production documents could be generated automatically when adjustments were made based on customer requirements. MuM's CAD consultants, who have been supporting Beer Grill for many years, put the company in contact with MuM's subsidiary, customX in Limburg. The configurator of the same name proved to be the best solution.
Rules for variants
customX does exactly what Beer Grill needs: Design rules and parameters can be used to define how products may look. Starting with the size of the display case, temperature control and lighting to possible accessories and the RAL colour of the decor, the possible combinations can be selected for each product line. The software immediately checks whether the entries are plausible and generates dimensional drawings, visualizations, design drawings, parts lists - in short, all the documents required first for the quotation and later for production.
Making complex things simple
In a training course lasting a few days, the designers at Beer Grill learned how to set up the rules. "Once you understand the principle, it's very simple," says designer Patrick David. Above all, you have to be able to switch from constructive thinking to variable thinking and look at your own products from a completely different angle. Rules have to be created and tested for each product line; this gets faster and faster as experience grows - after all, you don't need to acquire any programming skills because building rules in customX is real configuration too.
Configuring instead of constructing
In addition, the user interface has to be designed in such a way that users can make all the necessary entries in a logical sequence from their point of view. Finally, the configuration software is used by the sales representatives to develop the optimum solution in discussions with customers. This gives the customer a quicker visual idea of what his future showcases will look like, and the quotation is also quickly prepared. How much thought goes into each variant remains hidden from the outside world.
Digital knowledge memory
"To set up customX, you need to know the product range very well," says Benjamin Bihr, technical manager at Beer Grill. That is why the configurator is also a kind of knowledge management. "An experienced designer does not need to think long about what can be manufactured and how," explains Benjamin Bihr. "But when such an employee leaves the company, the knowledge is lost. Thanks to customX, we can keep this knowledge in the company now, and new employees can quickly be brought up to date with the product range".
Test, use, next step
The support provided by MuM and customX did not end with the training. In the beginning, the designers often had to consult with the specialists. Customer support via remote maintenance software TeamViewer offered fast, uncomplicated help. In the meantime, configuration is becoming easier and easier, and support is only needed for special cases. At the moment, the old configurator and customX are still running in parallel for test purposes, but the employees can already rely on the new system. When all the products have been converted to customX, the ERP system will also be connected so that customers can be sent quotations with all the necessary documents - i.e. dimensional drawings, installation instructions, etc. - directly from customX. When the customer orders, the parts lists for production are generated at the push of a button. Benjamin Bihr is optimistic: "We will be 30 to 40 percent faster - and that is a conservative estimate".

An experienced designer does not need to think long about what can be manufactured and how. But when such an employee leaves the company, the knowledge is lost. Thanks to customX, we can keep this knowledge in the company now, and new employees can quickly be brought up to date with the product range.
Benjamin Bihr
Technical Manager, Beer Grill AG
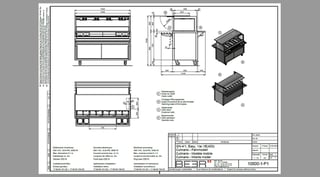