AKM-Tore GmbH
AKM-Tore GmbH takes several steps at once and, in addition to the introduction of drawings, also directly implements their digitalization.
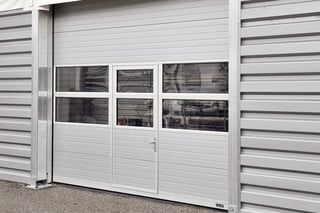
Targets
The introduction of configuration software should enable the generation of drawings and replace the old programmed solution for generating parts lists.
Implementation
At the same time as the changeover to CAD files for all orders and the introduction of ERP software, the decision was made in favor of customX, which now handles door calculation and document generation. After training, AKM took over maintenance itself.
Conclusion
The creation of drawings, parts lists and other documents was not only made possible, but also directly digitized and automated. customX creates enormous flexibility, as no external service providers are required for system maintenance.
From craft to industry
When AKM-Tore GmbH, located in the “Westerwald” decided to change the company's processes in 2007, it decided to take several steps at once and not only introduce CAD throughout for all orders, but also extensive automation with customX. What was previously mostly done on demand and with just a few sketches was now completely digitalized and largely automated.
Craft business
Before the introduction of customX, AKM worked like a typical craft company: High-quality, individual products were usually created without detailed documentation. This required an enormous amount of knowledge on the part of the employees in production. They were only supported by a self-programmed solution that provided simple parts lists. Otherwise, the sales department only passed on data on the existing opening and special requests from the customer via a form. Based on this, a principle sketch was created, in a few exceptions a CAD drawing, and the parts lists on which production was then based.
Maintenance effort for programming
Unfortunately, the parts list of the self-programmed solution was only very rudimentary and often even incorrect. Another problem became apparent after a few years of use: it was hardly possible to maintain the programmed application, as the technical basis had changed in the meantime and the program had become quite complex over time. In-depth programming knowledge was essential for making changes. The result would have been considerable effort - both in terms of time and money.
Cost and time pressure in the door industry
At the same time, of course, the market had evolved and every customer now expected a DWG drawing at a very early stage and not just a list of the door data and possibly sketches. Due to the increasing individualization in most markets - including the door industry - the cost and time pressure was and still is extremely high. Customers today assume that individual planning will not take any longer and will deliver the same documents as a standard product.
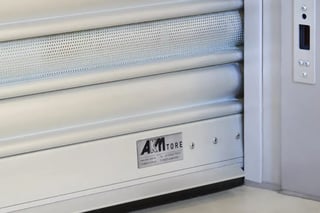
Development into an industrial company
It therefore made sense to expand the CAD application introduced in the nineties in order to be able to create exact drawings for all orders. This was common practice at the time (2007) and many companies opted for this approach. However, AKM realized very early on that the effort involved in drawing every single door would have been far too high. Those responsible at AKM not only wanted CAD, they also wanted to achieve the automation of variant design directly, including all associated documents, in order to develop AKM into a modern industrial company. The decision was made - in addition to the introduction of ERP - in favor of the configuration software customX from the Man and Machine Group.
Complex calculations
customX was implemented and connected directly to the ERP system. Initially, there was a little resistance from the sales department, which was used to being able to start production on demand with just a few specifications. This quickly subsided once it became clear how the new solution had improved processes. Today, all sectional doors are calculated with customX and parts lists and 2D drawings are generated.
What sounds so simple - "I have a hole, a door of the right size has to go in there" - is actually a complex calculation, as not only do the height and width have to be adjusted, but panels have to be precisely planned and guide rails calculated. After all, the door should not just fit, but also be well integrated into the style of the building. And, of course, it should also work!
Use for technical planning
Today, customX is used internally by the technical department to plan the doors and generate documents, which in turn form the basis for production. One advantage for production is that the employees there no longer need to have a huge amount of specialist knowledge. The training of new employees is correspondingly fast. The search for new employees is also simplified, which is invaluable, especially in times of a shortage of skilled workers.
A giant step
Around 2,000 - 3,000 doors are planned and manufactured at AKM every year. In ten years, 490,000 documents have been created automatically with customX. It is obvious that this quantity could not have been achieved manually in a medium-sized company with 100 employees. At the same time, you can always be sure that the documents are 100% correct. However, it is difficult to estimate the time saved by the introduction of customX in the case of AKM, as it would be comparing apples with oranges. After all, it was only with the introduction of customX that drawings were created for each individual door.
Maintenance effort minimized
Of course, the whole thing could also have been solved using individual programming. But then a decisive advantage of customX would have been lost: The maintenance of this system can be taken over by technical staff. Even after many years of operation, this is possible without any problems, as the software is a standard application that only requires a simple update every now and then. Tobias Käsgen, project manager at AKM, is also pleased that changes can be made in this application without any programming knowledge: "Expensive programmers, who are also not readily available, are not needed, which makes customX very flexible and cost-saving." A customX employee is only called in for major changes, and this is quite rarely the case.

Expensive programmers, who are also not readily available, are not needed, which makes customX very flexible and cost-saving.
Tobias Käsgen
Project Manager, AKM-Tore GmbH
Outlook
One such adaptation is the planned expansion of the ERP interface. The connection to ERP is already in place and the parts lists are also generated via this interface, but the connection is to be much more intensive. Another important project coming up soon is the introduction of BIM and the associated switch to 3D. This means that customX will remain a key component of AKM's software landscape in the future and will further create enormous efficiency benefits.